-
Chanel’s Le Volume Révolution de Chanel mascara features a granular-surfaced eyelash wand.
-
Dutch designer Iris van Herpen is at the forefront of the 3-D phenomenon.
-
German high-end prêt-à-porter label Marc Cain is blazing a trail in 3-D knits.
-
Marc Cain uses Stoll 3-D–knitting machines that feature traditional knitting needles but only one thread.
-
The Y-3 Runner 4D from Adidas and Yohji Yamamoto has a 3-D-printed midsole.
-
The Y-3 Runner 4D’s 3-D-printed technology.
The Future of 3-D Fashion
Fashion x science.
Just like the sewing machine revolutionized clothing production in the late 18th century, 3-D printing is causing a stir in the modern sartorial world. While the 3-D printer hasn’t become a household appliance—not yet—this curious new technology is courting the fashion industry in high style.
Fashion editors really took notice when Demna Gvasalia presented his autumn 2018 collection for Balenciaga. Experimental in an accessible and discreet way, the influential designer used 3-D scans to custom fit his models with lightweight foam moulds that were, themselves, also 3-D printed. Virtually seamless, each hourglass shell was finished with a single layer of tweed or houndstooth, representing a fresh, new take on the traditional fall coat.
Dutch designer Iris van Herpen is at the forefront of the 3-D phenomenon. Sometimes collaborating with Toronto-based artist and architect Philip Beesley, the former dancer has sculpted wearable masterpieces in fantastical, organic themes ranging from shells to soap bubbles. Time magazine hailed her 3-D dresses, which she debuted in 2011, as one of the best inventions of that year. Never late to the party, Karl Lagerfeld has dipped his gloved hands into 3-D technology. In his autumn 2015 haute couture collection for Chanel, the Kaiser presented 3-D–printed versions of the maison’s classic tweed ensembles.
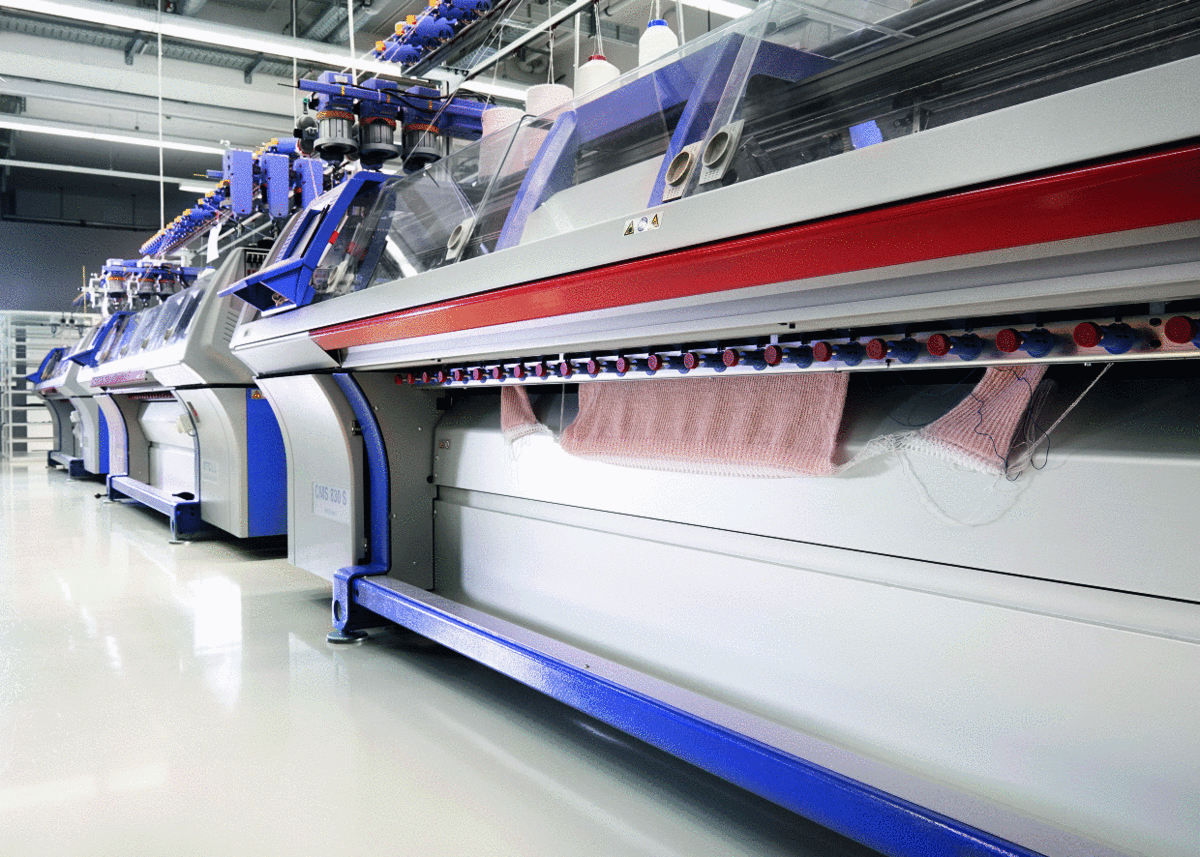
Marc Cain’s knits are created on Stoll 3-D–knitting machines.
In 2016, van Herpen and Chanel were showcased in Manus x Machina: Fashion in an Age of Technology at the Metropolitan Museum of Art, a timely exhibit that explored and questioned the dichotomy between the perceived luxury of garments made by hand and the soulless nature of those made by machine. While van Herpen’s magnificent portfolio went some ways to debunking the theory, her works are nevertheless more at home in museums or draped upon Lady Gaga or Björk than in the average woman’s closet.
“In terms of fashion, the future depends on the evolution of 3-D printers that will be able to print fabrics that are soft, resistant, and washable.”
Science is also steering our attitudes in new directions. While haute couture is highly customized to elite individuals, new Adidas technology aims to deliver custom-fitted high-performance running shoes to the masses. Sneaker aficionados got a soft feel for this last June when the label introduced the Y-3 Runner 4D from Adidas and Yohji Yamamoto, which has a spectacular web-like, 3-D–printed midsole. It is a designer upgrade of the craze-inducing Futurecraft 4D, introduced just a few months earlier. Adidas hopes to expand the technology to incorporate fully personalized 3-D scans of feet for optimized fit and performance—the ultimate in made-to-measure footwear.
This fall, Chanel will prove that 3-D prints have advanced well beyond prototypes and can be marketed as final products in the world of beauty. Eleven years in the making, the label is launching Le Volume Révolution de Chanel, a mascara whose granular-surfaced eyelash wand (all the better for “lash adherence and product deposit” with “honeycomb micro-cavities” and “millimetre-scale arrangement of bristles,” ensuring the perfect dose with each application) is the first 3-D–printed mascara brush industrialized on a large scale.
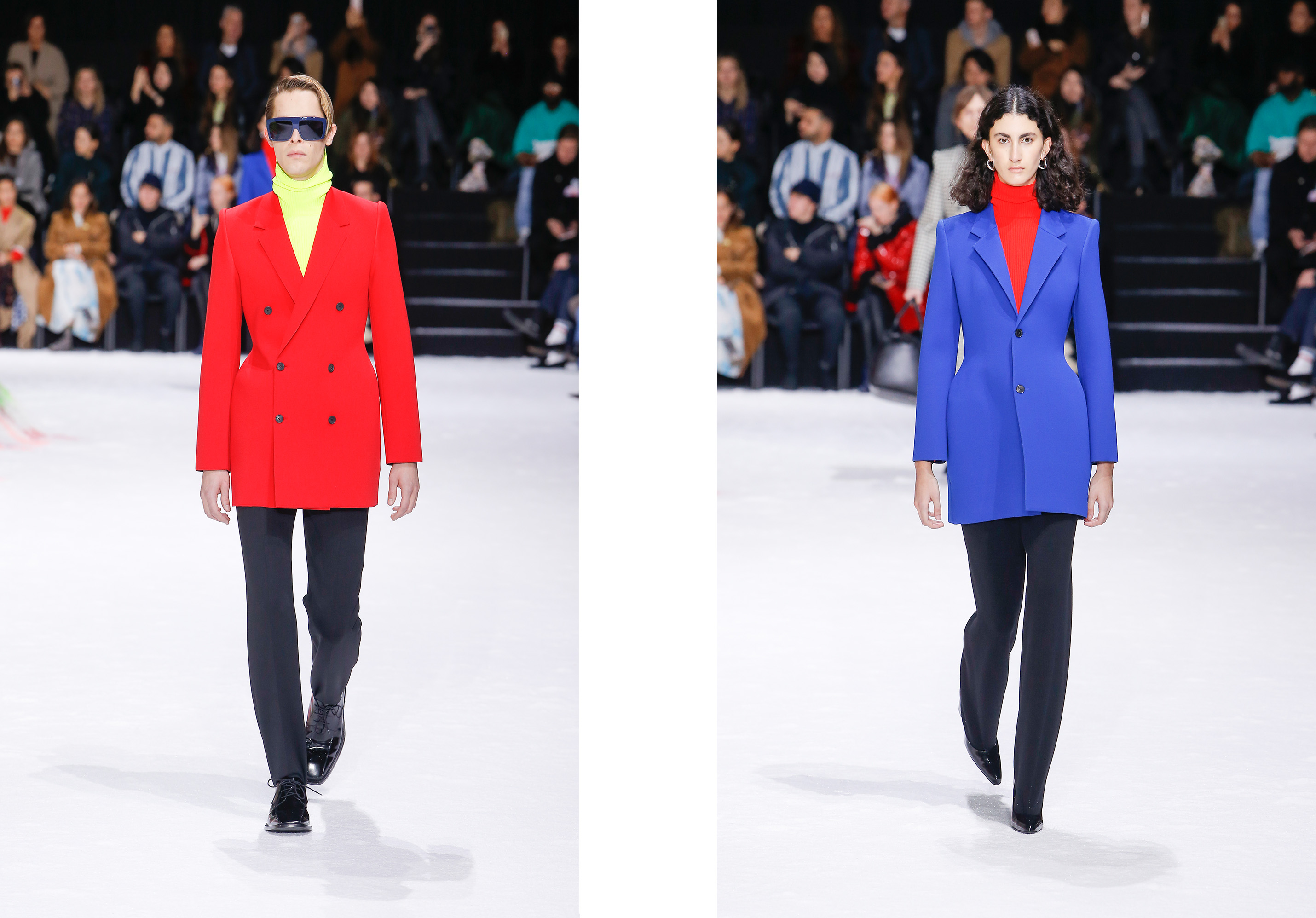
Balenciaga’s impeccable 3-D tailoring.
When it comes to wide-scale fashion production, German high-end prêt-à-porter label Marc Cain is blazing a trail in 3-D knits. The company uses Stoll 3-D–knitting machines that feature traditional knitting needles but only one thread, transforming a pattern into a garment in a single step. Says founder Helmut Schlotterer, “The 3-D knitted pullover emerges from the knitting machine in just a single production operation.” The end product has no seams and because there are no cutaway parts, there is zero waste.
Old-school habits and attitudes, however, are still ubiquitous in the fashion landscape. Educational institutions such as ESMOD (École supérieure des arts et techniques de la mode) and IFM (Institut français de la mode) in Paris, the world’s fashion capital, overlook 3-D applications in their core curriculum, where the focus of handiwork is still the benchmark of luxury. Similarly, at Parsons School of Design in New York, 3-D application doesn’t make it into core classes, though inspired students can opt to take a 3-D atelier. Here in Canada, Jocelyn Bellemare, a professor at the Université du Québec à Montréal, stresses that further exploration is necessary. “In terms of fashion, the future depends on the evolution of 3-D printers that will be able to print fabrics that are soft, resistant, and washable.”
At Ryerson University in Toronto, fashion professor Danielle Martin echoes Bellemare’s sentiments, adding that the “big gaps to be filled” in 3-D printing for the ready-to-wear industry are “comfort, sustainability, and price.” Martin is leading a research project called Fashion Design for DIY that allows “the participation of the end user to design part of his garments according to his or her taste, choice and values.” Will 3-D technology eventually allow us to design and print our own garments at home? Stay tuned—this may be closer than you think.
_________
Never miss a story. Sign up for NUVO’s weekly newsletter.